Top-Down-Modellierung im 3D-CAD
Einsatzmöglichkeiten, Vorteile und Grundlagen der Top-Down-Methode
Links zum Thema:
Das Video zur Top-Down-Modellierung bei Youtube oder DailyMotion und die Kurzpräsentation als PDF.
Automatisierung von CAD-Modellen mit der Top-Down-Methode
Dieser Tage wird viel über Digitalisierung und Automatisierung aller möglichen Lebensbereiche geredet und geschrieben. Bei Gesprächen höre ich dagegen manchmal "Konstruktionsarbeit kann ja nicht automatisiert werden". Das sehe ich allerdings nicht so. Auch in der klassischen CAD-Konstruktion gibt es einiges an immer gleicher Fleißarbeit, die wir gut den Computer für uns machen lassen können, wenn wir CAD-Konstrukteure unsere Arbeitsweise daraufhin ausrichten. Eine Möglichkeit dazu ist die Top-Down-Methode.
Top-Down-Modellierung ist an sich eine schon lange bekannte CAD-Methode und wird im Grundsatz auch von den Herstellern der 3D-CAD-Systeme dokumentiert und mittels darauf ausgerichteter Funktionen unterstützt, wobei sich das Engagement in diesem Bereich zwischen den Anbietern stark unterscheidet.
Obwohl es eine sehr zeitgemäße Methode ist und viel über Effizienz geredet wird, führt diese Form des Modellaufbaus nach meinem Eindruck bisher eher ein Nischendasein, nur wenige Konstrukteure scheinen so zu arbeiten.
Ich möchte interessierten 3D-CAD-Konstrukteuren hier die Top-Down-Methode, insbesondere in Form der Skelettmodellierung, näher bringen, weil ich sie sehr spannend und nützlich finde, und sie uns helfen kann, unsere Effizienz zu steigern und dadurch letztlich auch unsere Arbeitsplätze zu erhalten.
Das Thema an sich ist einigermaßen unabhängig davon, welches CAD-System man benutzt, denn die Grundprinzipien gelten für alle Systeme gleichermaßen. Meine Beispiele zeige ich in Inventor. Wenn etwas in Creo grundlegend anders ist, werde ich das parallel erwähnen. Top-Down-Modellierung an sich dürfte in allen gängigen 3D-CAD-Systemen umsetzbar sein, Solid Works z. B. macht da auch Werbung mit (das Stichwort ist hier "intelligente Baugruppen"), da weiß ich aber nicht im einzelnen, wie es bedient wird.
Wofür ist Top-Down-Modellierung gut geeignet?
Top-Down-Modellierung, insbesondere Skelettmodellierung, ist gut, um schnell konsistente, flexible und für die Detailkonstruktion nahtlos weiterverwendbare Entwürfe aufzubauen sowie allgemein effizient anpassbare Baugruppen zu erstellen.
Meiner Meinung nach ist die Methode sinnvoll für alle Baugruppen, bei denen Teile oder Unterbaugruppen über Schnittstellen miteinander verbunden sind, also so ziemlich jede Konstruktion. In Bild 1.1 beispielhaft eine Gleitlagerung in Skelettmodellierung:
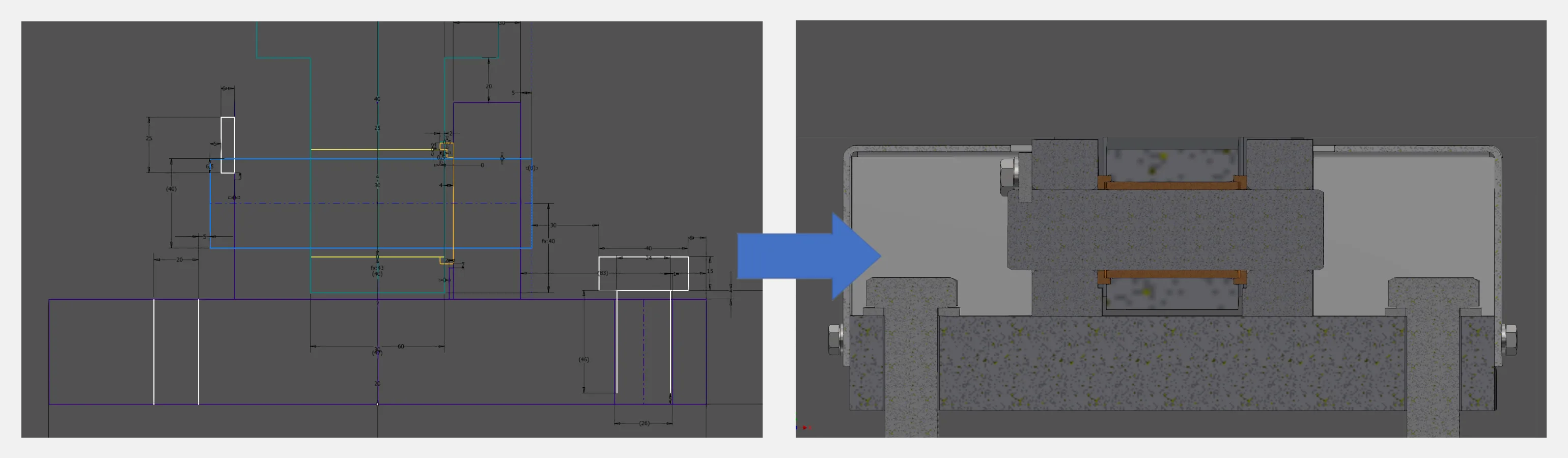
Auch zur Synchronisation von Bauräumen oder Schnittstellen verschiedener Anlagenteile kann sie sehr nützlich sein. Bei Bild 1.2 musste um den roten Störbereich herumkonstruiert werden, bei Bild 1.3 eine vorhandene Anschraubfläche weiter verwendet werden:
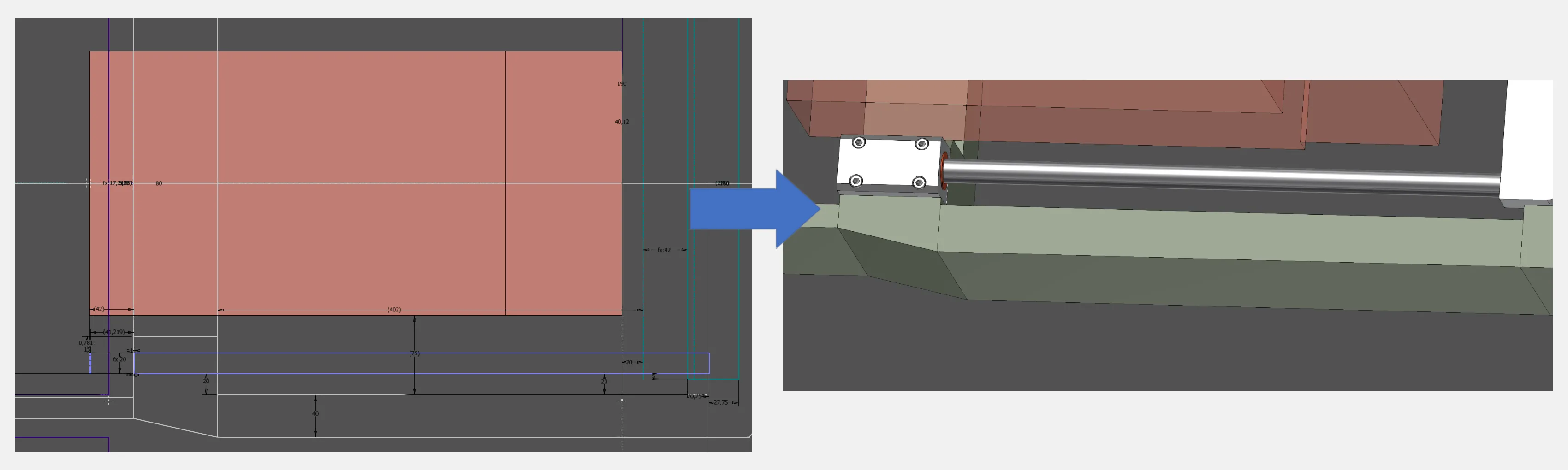
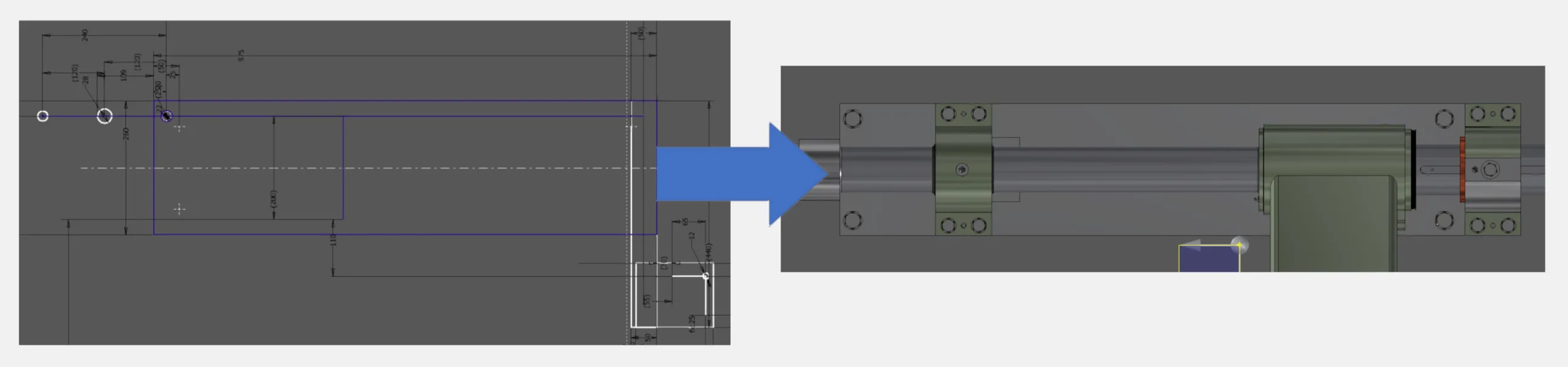
Ihre Vorteile spielt die Top-Down-Modellierung besonders dann aus, wenn Modelle nach der erstmaligen Erstellung noch verändert werden sollen. Wenn also im Lauf der Entwurfsphase Maße variiert werden oder ein Kunde sich nach Präsentation des Entwurfs Anpassungen wünscht, kann man mit wenig Aufwand die Konstruktion anpassen und dabei relativ sicher sein, dass nach der Änderung noch alle Teile zusammen passen. Bild 1.4 zeigt die Änderung einer Gleitlagerung durch Verändern von einigen Maßen im Skelett.

Auch, wenn man eine prinzipiell gleiche Konstruktion in verschiedenen Baugrößen oder mit auftragsweise angepassten Maßen ausführen oder insgesamt skalieren möchte, spart die Methode viel Arbeit. In einem gut aufgebauten Top-Down-Modell kann man bei all diesen Szenarien mit sehr wenig Aufwand durch Eingabe weniger Maße Anpassungen vornehmen, die dann durchgängig konsistent in alle abhängigen Teile übernommen werden.
Gängige Anwendungsfälle sind zum Beispiel:
- Lagerungen, bei denen Gehäuse, Deckel, Wellen etc. von der Wahl des Wälz- oder Gleitlagers abhängen
- Schweißkonstruktionen, die aus maßlich voneinander abhängigen Teilen bestehen
- Bewegliche Teile, deren Schnittstellen von verschiedenen Bewegungspositionen abhängen
- Konstruktionen, bei denen Bauraumgrenzen beachtet werden müssen
- Verschraubungen (Bild 1.5)
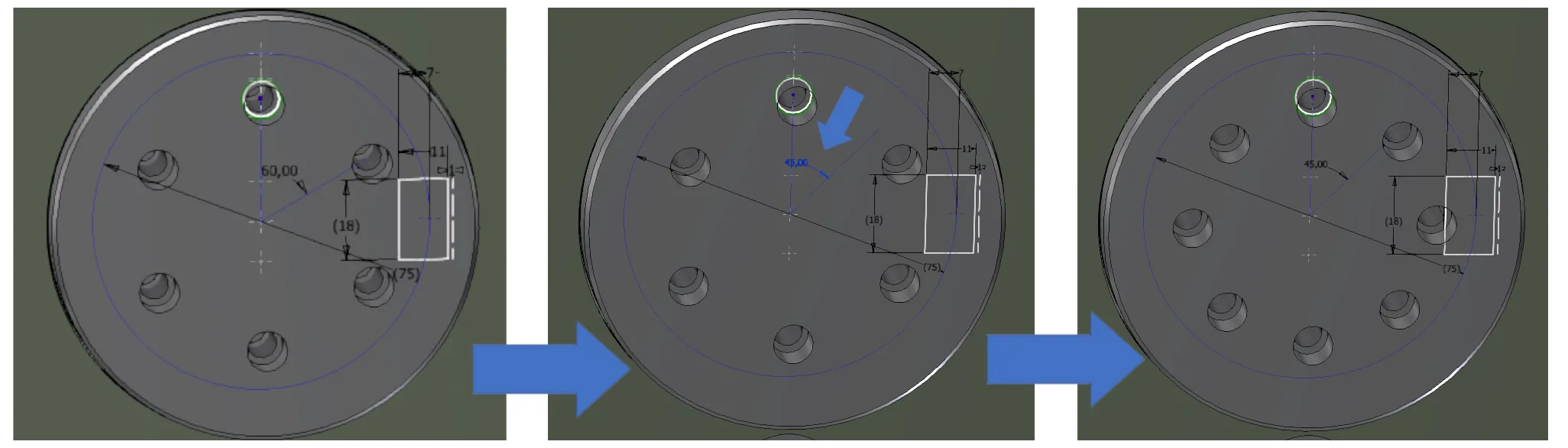
Die Top-Down-Methode bietet sich also besonders an für:
- Zusammenhängenden Aufbau von Baugruppen, bei denen verschiedene Teile oder Unterbaugruppen gemeinsame Schnittstellen haben
- Schnelle Erstellung flexibler, konsistenter Entwürfe
- Baugruppen, die nach der Erstellung skaliert oder maßlich angepasst werden sollen
Wie funktioniert Top-Down-Modellierung?
Top-Down-Modellierung funktioniert grundsätzlich so, dass in der Baumhierarchie der Baugruppenmodelle auf der jeweils höheren Hierarchieebene Elemente definiert werden, die dann als Basis für die nächstniedrigere Ebene verwendet werden. Dafür werden sogenannte Skelettteile verwendet. Zu jeder Baugruppe gehört ein Skelettteil, in dem meist in Form von Skizzen oder Arbeitselementen die für diese Baugruppe wichtigen Maße, Geometrien, Zusammenhänge und Zustände definiert sind (Bild 2.1). Prinzipiell sind auch Flächen- oder sogar Volumenkörper im Skelett möglich, aber ich denke, die haben meist mehr Nachteile als Vorteile. Für die Anlagenlayoutplanung reicht manchmal auch ein sehr grobes Skelett, mit dem nur Ebenen, Achsen oder Koordinatensysteme zur Platzierung der Einzelanlagen und Schnittstellen übergeben werden. Für Maschinen und Vorrichtungen kann es dagegen sinnvoll sein, alles bis hin zu den Gewindegrößen im Skelett zu definieren. Normteile sind leider in Inventor und Creo nicht ohne Weiteres automatisierbar, die muss man noch von Hand ändern, oder sich größere Skripte schreiben.
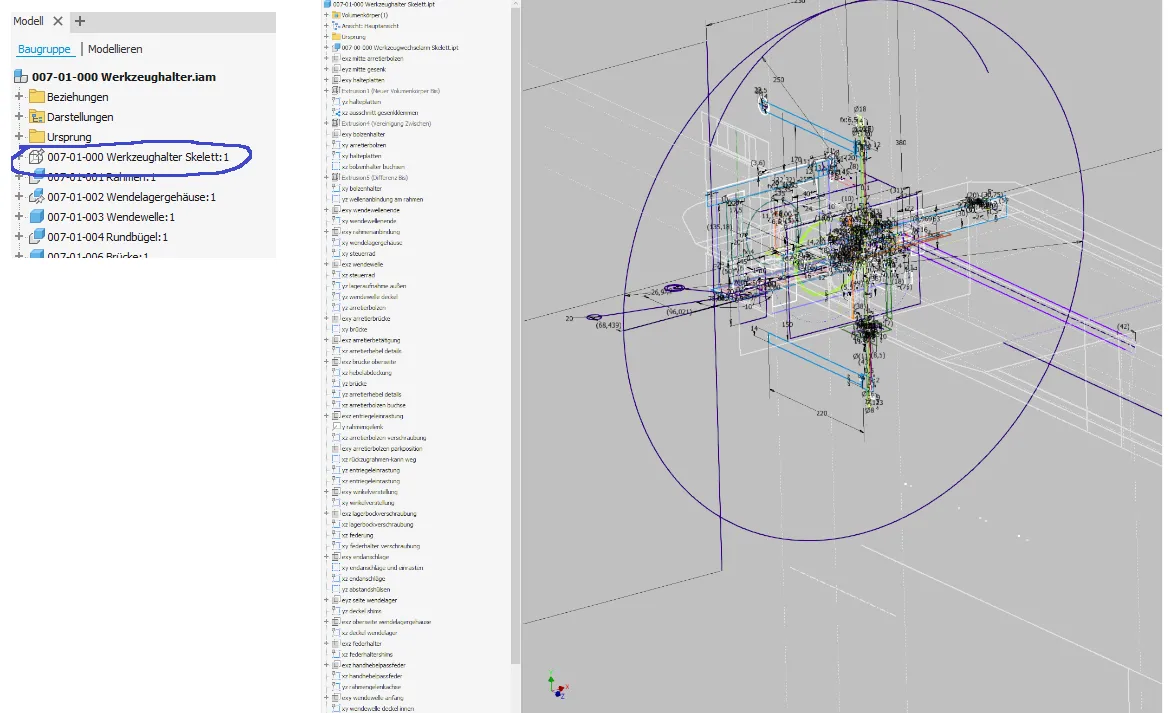
Wenn viele Skizzen sichtbar sind, sieht das auf den ersten Blick sehr unübersichtlich aus. Normalerweise schaltet man deshalb nur die Skizzen sichtbar, die man gerade braucht, was dann meist sehr überschaubar ist (Bild 2.2 und 2.3):
Die in dieser Baugruppe eingebauten Teile oder Unterbaugruppen übernehmen dann die relevanten Elemente des Skeletts sozusagen als externe Referenzen und bauen darauf auf. Bei Inventor heißt die dafür verwendete Funktion "abgeleitetes Bauteil" und ist sehr komfortabel, bei Creo ist es die Kombination aus "Publiziergeometrie" und "Kopiegeometrie" und ist nicht ganz so komfortabel. In beiden Fällen wählt man nur die Elemente aus dem Skelett aus, die im Teil gebraucht werden. Nützlicher Nebeneffekt ist, dass man meist im Einzelteil auch die Schnittstelle der angrenzenden Teile sehen kann. Bild 2.4 verdeutlicht den Informationsfluss von der Skelettskizze über die Funktion "abgeleitetes Bauteil" in die Einzelteile.
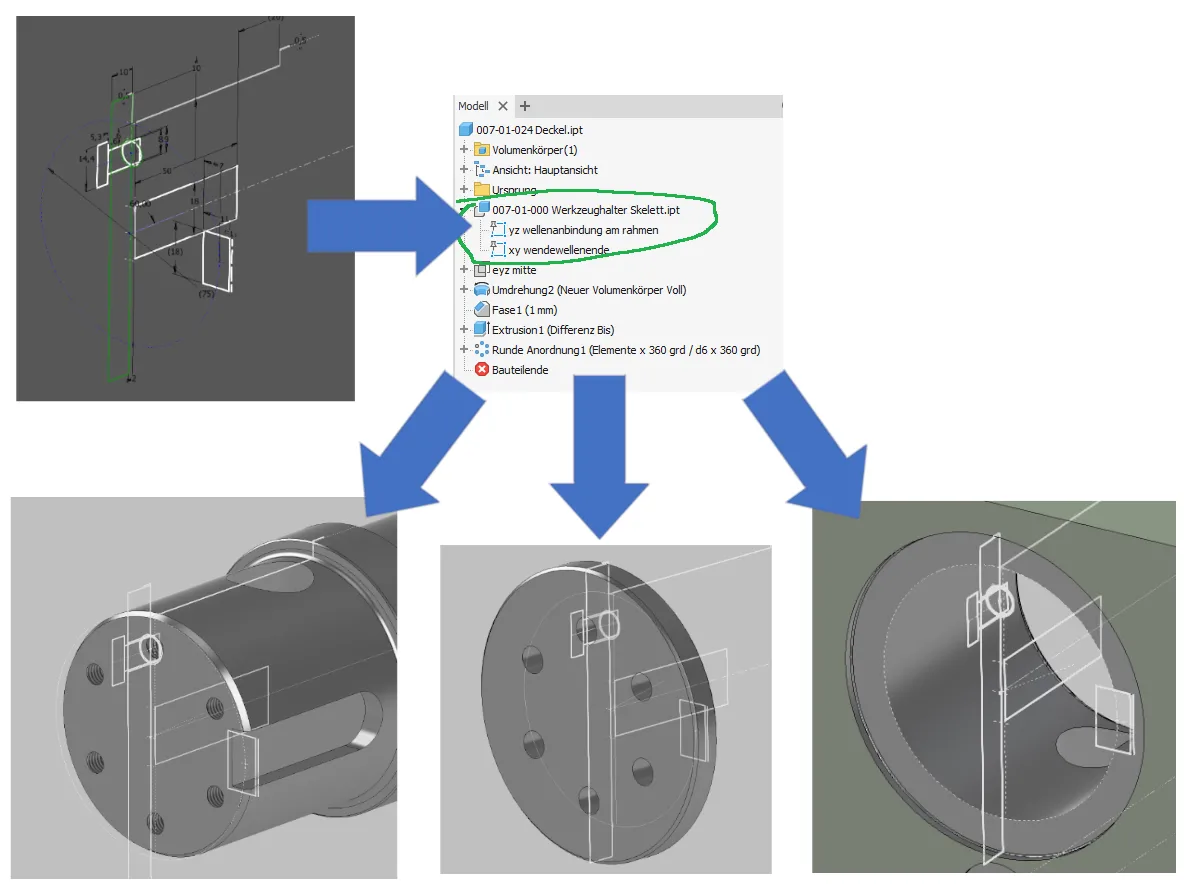
Alle Maße, die im Skelett definiert wurden, werden entsprechend im Einzelteil oder der Unterbaugruppe nicht mehr definiert, sondern nur noch übernommen.
Dadurch entsteht ein redundanzfreies Gesamtmodell, denn Schnittstellenmaße für die Verbindung mehrerer Teile müssen nicht mehr in jedem Teil einzeln festgelegt und manuell übertragen werden, sondern werden einmal im Skelett für alle beteiligten Teile / Unterbaugruppen festgelegt.
Besonders viel Mehrfacharbeit lässt sich auf diese Weise sparen bei der Konstruktion von:
- Verschraubungen
- Schweißteilen
- Lagerungen
- Steckverbindungen
- Abdeckungen und Deckeln
- Beweglichen Teilen mit mehreren relevanten Positionen
- ...
Vorteile der Top-Down-Modellierung
Die Vorteile von Top-Down-Modellierung gegenüber unabhängigen Einzelteilen sind ähnlich, wie bei einer aus 3D abgeleiteten Zeichnung gegenüber einer 2D-Zeichnung: Bei einer aus 3D abgeleiteten Zeichnung muss man Änderungen nur einmal im Teil machen und alle Ansichten, egal wie viele, werden vom System aktualisiert, wo im 2D jede Ansicht einzeln manuell geändert werden müsste. Bei einer mittels Top-Down-Methode erstellten Baugruppe muss man Änderungen nur einmal im Skelett machen und das System aktualisiert alle abgeleiteten Teile, wo bei einer konventionellen Baugruppe jedes Teil einzeln manuell geändert werden müsste.
Zeitersparnis
- Bei der Modellerstellung werden Schnittstellen nur einmal für alle betroffenen Teile zusammen erstellt.
- Bei Maßänderungen oder Skalierung werden betroffene Maße nur einmal bearbeitet.
- Man braucht nur eine Modellstruktur für ein Produkt, die den aktuellen Stand der Entwicklung enthält, und kann unterschiedliche Größen und Varianten davon ableiten.
Fehlervermeidung
- Fehler bei der Maßübertragung zwischen Teilen entfallen, weil jedes Maß nur einmal existiert.
- Abweichungen durch Modellierungs- oder Zusammenbaufehler sind durch Überlagerung mit dem Skelett leicht erkennbar.
- Zusammenhänge werden funktionsgerecht so definiert, wie sie logisch zusammen gehören.
- Arbeiten mehrere Bearbeiter an einem Projekt, werden die Schnittstellen zwischen ihnen durch die Skelette fortlaufend synchronisiert.
Hohe Flexibilität bei Entwürfen
- Baugruppenmodelle können vollständig aufgebaut werden, ohne dass Eingangsgrößen genau bekannt sind, weil nachträgliche Aktualisierung einfach möglich ist.
- Für Simulationen oder Visualisierungen können Grundgeometrien als Grobkörper abgeleitet werden, ohne dass zuerst Einzelteile erstellt und zusammengebaut werden müssen.
Verbesserte Baugruppenorganisation
- Instabile Einbaureferenzen für importierte Modelle können durch Arbeitsgeometrie im Skelett ersetzt werden.
- Verschiedene Bewegungszustände können auf Basis der vorhandenen Geometrie übersichtlich im Zusammenhang dargestellt und bearbeitet werden.
- Vorgegebene Anschlussmaße der Umgebung können als Eingangswerte im Skelett verwendet und so zuverlässig eingehalten werden.
- Erkennung von potenziellen Gleichteilen sowie Übertragung und Absicherung von Schnittstellenmaßen ist im Skelett sehr einfach.
Nachteile
Es hat natürlich alles seinen Preis: Auch diese Methode hat Nachteile, sonst würde ja jeder schon damit arbeiten:
- Sehr sorgfältige Auswahl der Referenzen bei der Modellerstellung erforderlich
- Es muss sehr sorgfältig auf geometrisch stabile Skizzen geachtet werden
- Aufwand bei funktionalen Änderungen kann größer werden (z. B. rundes Teil wird eckig, Beteiligung von Teilen an Schnittstellen ändert sich, ...)
- Einarbeitungsaufwand sowohl in die Methode als auch in eine von anderen Konstrukteuren erstellte Top-Down-Struktur
- Herkunft von Maßen und Geometrien muss über die Hierarchieebenen gesucht werden, wenn etwas geändert werden soll
- Einige wichtige Grundregeln müssen bei der Modellerstellung zwingend diszipliniert befolgt werden
- Bei Änderungen kann Fehlersuche erforderlich sein, weil Elemente aufgrund kleiner Fehler, oft bei der Referenzierung, fehlschlagen
Intuitiv vermuten Anwender Nachteile für die Verarbeitungsgeschwindigkeit beim Laden der Modelle, aber hier gibt es meines Wissens keine Nachteile: Bei der Rechenperformance sind Top-Down-Modelle normalerweise nicht schlechter sondern aufgrund der deutlich reduzierten Variablenanzahl und zwangsweise saubereren Struktur eher besser als konventionelle Modelle. Ich selbst jedenfalls habe in etlichen Jahren noch nicht erlebt, dass Modelle dadurch langsam geworden wären.
Voraussetzungen für die Anwendung der Top-Down-Modellierung
- Für die Erstellung stabiler Top-Down-Modelle sind solide Kenntnisse im verwendeten CAD-System notwendig.
- Generell muss verbindlich definiert werden, bis zu welchem Detaillierungsniveau im Skelett gearbeitet wird.
- Konventionen für die Struktur von Baugruppen und die Kenntlichmachung von Skizzen und Arbeitselementen müssen erstellt und sehr konsequent eingehalten werden.
- Vorhandene konventionelle Modelle müssen möglicherweise in die Top-Down-Struktur eingehängt oder dafür neu erstellt werden.
- Für die Anpassung vorhandener Top-Down-Modelle hingegen reichen Grundkenntnisse, eine Einweisung in die Methode und Geduld beim Suchen der benötigten Maßquellen. Die Bereitschaft, eine grundlegend andere Arbeitsweise anzuwenden, muss allerdings vorhanden sein.
Fazit, Schlusswort
Trotz gegenläufiger Effekte durch Beseitigung von Referenzierungsfehlern oder Mehraufwand bei grundlegenden funktionalen Änderungen von Geometrien bringt die Top-Down-Methode, richtig angewandt, in vielen Fällen eine große Verbesserung der Effizienz. Konstruktionsarbeit kann also teilweise doch automatisiert werden, es gibt einiges an Fleißarbeit, die wir dadurch vermeiden können.
So, dies war der erste Abschnitt hier im Bereich "CAD-Tutorials". Wenn es positive Rückmeldungen dazu gibt, werde ich weitere Kapitel hinzufügen.
Falls Sie tiefergehende Beratung zu CAD-Methoden benötigen, klicken Sie bitte auf Kontakt.
Sie können auch gerne die Kurzpräsentation zum Thema herunterladen. Sie darf in unveränderter Form unter Nennung der Quelle frei verwendet werden, auch kommerziell (Lizenz: CC BY-ND).
Links anklicken um in die Zwischenablage kopieren:
Diese Seite: https://r-kon.de/cad-top-down-modellierung.php
Das Video: https://youtu.be/ObaCM5vhklA (Youtube) / https://dai.ly/x8pbl1m (DailyMotion)